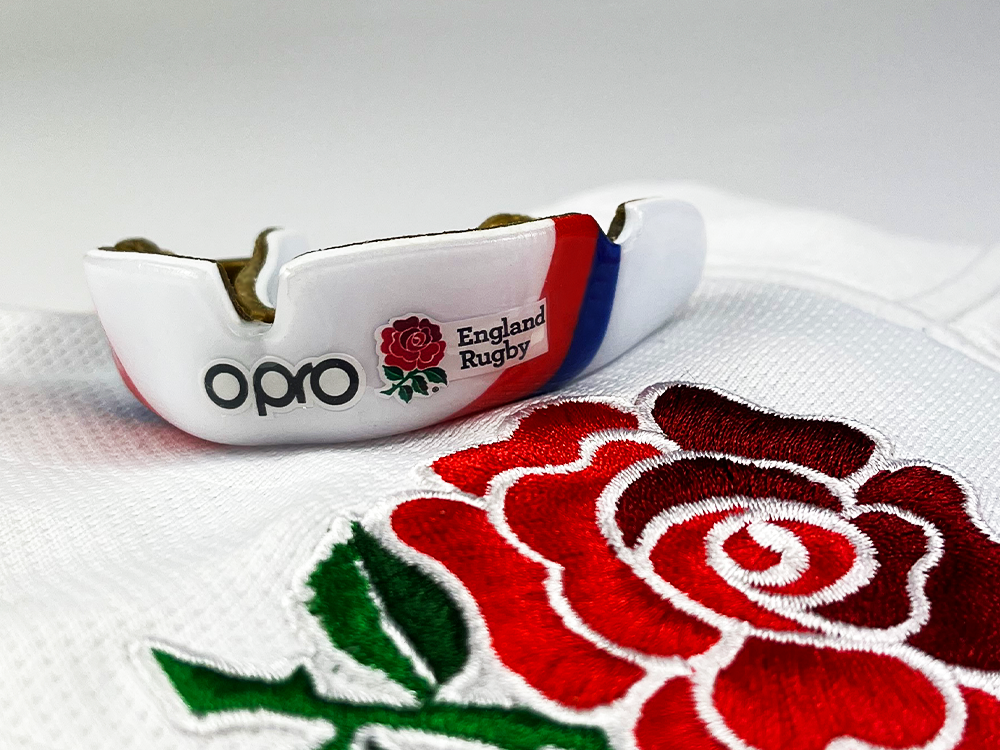
In the high-paced environment of sports safety equipment, the collaboration between OPRO, the pioneering force behind custom-fit EVA mouthguards, and Condale Plastics, stands as a testament to innovation, quality, and dedication to excellence.
This case study, comprising of a recent interview with OPRO’s Product and Production Director, delves into the intricacies of manufacturing cutting-edge mouthguards and the integration of a highly specialist antimicrobial component inside the plastic itself – highlighting why this unique EVA is safe and highly suited for this application within the mouth.
The Journey of Crafting Custom-fit EVA Mouthguards
The journey of crafting a custom-fit sports protection mouthguard begins with acquiring dental impressions through various means: home impression kits, dental impressions, or dental scans. “The dental impression can either be an impression that somebody takes at home themselves using one of our home impression kits, or it can be a dental impression or scan that a dentist has taken,” their director explains, emphasising the various options at these initial steps.
Once received, these impressions are digitised using proprietary CAD software, a process pivotal for transforming a physical impression into a model ready for manufacturing. “We scan the impressions in order to get a scan. All of the scans are then CADed using our software,” highlighting the seamless integration of technology in crafting precision-based dental models.
These files are sent to a third-party company for 3D printing, returning as tangible models used to manufacture each custom-fit mouthguard. The application of barcodes onto each model is a crucial step, ensuring that every detail of the customer’s order, from colour preferences to impact protection level, is accurately recorded and tracked through the whole production process.
A fascinating aspect of the manufacturing process involves the creation of mouthguards with unique designs. “So if we want to make a stripe design or any of our more exotic ones, we take different widths of the different coloured pieces of EVA and we heat it up. Because it is EVA, when it’s heated it will bond to itself,” their director shared, unveiling the creative process behind each bespoke piece.
The thermoforming process, involving heat and pressure, shapes the mouthguard to its final form. “So we are basically heating up the EVA blank in machines that are called Drufomats. When the material reaches the desired temperature, it starts to droop before then being forced down over the dental model,” their director explained, providing a glimpse into the transformative journey from a simple EVA blank to a protective mouthguard.
Automation has significantly enhanced this process, with the introduction of collaborative robots or “cobots” that assist in precision cutting, flaming and buffing, ensuring each mouthguard not only meets functional requirements but also achieves a smooth finish. “Then we have some buffing machines, which have got milling wheels. They’re like giant sandpaper discs. They then buff off the rough edges,” their director said, indicating the meticulous attention to detail.
Quality control is paramount, with multiple stages of checks ensuring that each product adheres strictly to the ordered specifications. This rigorous process is crucial, especially when producing instrumented EVA mouthguards for sports impact assessments – a newer venture that has seen the OPRO partner with a range of providers of electronics boards and collaborating with international sporting bodies and teams.
Integration of Biomaster Antimicrobial Technology
A cornerstone of OPRO’s product innovation, and a result of the collaboration with Condale Plastics, is the incorporation of Biomaster antimicrobial technology. Biomaster is used to inhibit the growth of bacteria, fungi, mould, and other harmful microorganisms. It utilises silver ion technology, recognised for its antimicrobial properties, to offer protection against microbes. This technology works by disrupting cell walls, interfering with enzyme production, and preventing DNA replication of microbes, thereby stopping their growth and spread.
Biomaster is integrated into the materials during the manufacturing process, ensuring that the antimicrobial properties last for the product’s lifetime. This approach makes Biomaster different from coatings that might wear off over time. So it’s particularly suitable for products that require high standards of hygiene and microbial control.
Biomaster’s safety profile is another key aspect, as it is skin-safe and food-safe, making it suitable for a wide range of applications without adverse effects on human health. Its effectiveness and regulatory compliance have been validated through independent testing and certifications, including registration with the Biocidal Products Regulation (BPR) in the UK and Europe, the Food and Drug Administration (FDA) in the US, and approval by the Environmental Protection Agency (EPA).
Collaborative Excellence with Condale Plastics
Exploring new materials for these innovative mouthguards, OPRO is conducting trials with Condale Plastics to test a softer variant of EVA. This exploration into material properties underscores the continuous pursuit of excellence and customisation. “We are doing some testing with Condale Plastics, extruding a new material, which is a slightly softer EVA than we normally use,” their director noted, showcasing the collaborative effort to enhance product quality.
The relationship with Condale Plastics is characterised by mutual respect and cooperation, particularly in times of crisis, such as the challenges posed by COVID and global supply chain disruptions. Their director praised Condale Plastics for their flexibility and support: “They’re very open and willing to help out. Sometimes, if I’ve got a rush job, they’ve been willing to shift their manufacturing schedules around, they will help out.”
Awards and Recognition
This partnership, bolstered by innovation and a shared commitment to quality, has contributed significantly to the OPRO’s accolades, including two Queen’s Awards. These awards, especially the one in 2007 linked closely to the custom-fit EVA mouthguards, celebrate OPRO’s excellence in its field and its successful collaboration with Condale Plastics.
The alliance between OPRO and Condale Plastics epitomises a commitment to innovation in sports safety equipment. Through the integration of Biomaster antimicrobial technology and the exploration of new materials, OPRO has become a world-renowned leader. This case study not only highlights their achievements but also serves as an inspiration for future collaborations aimed at enhancing product quality and consumer safety.