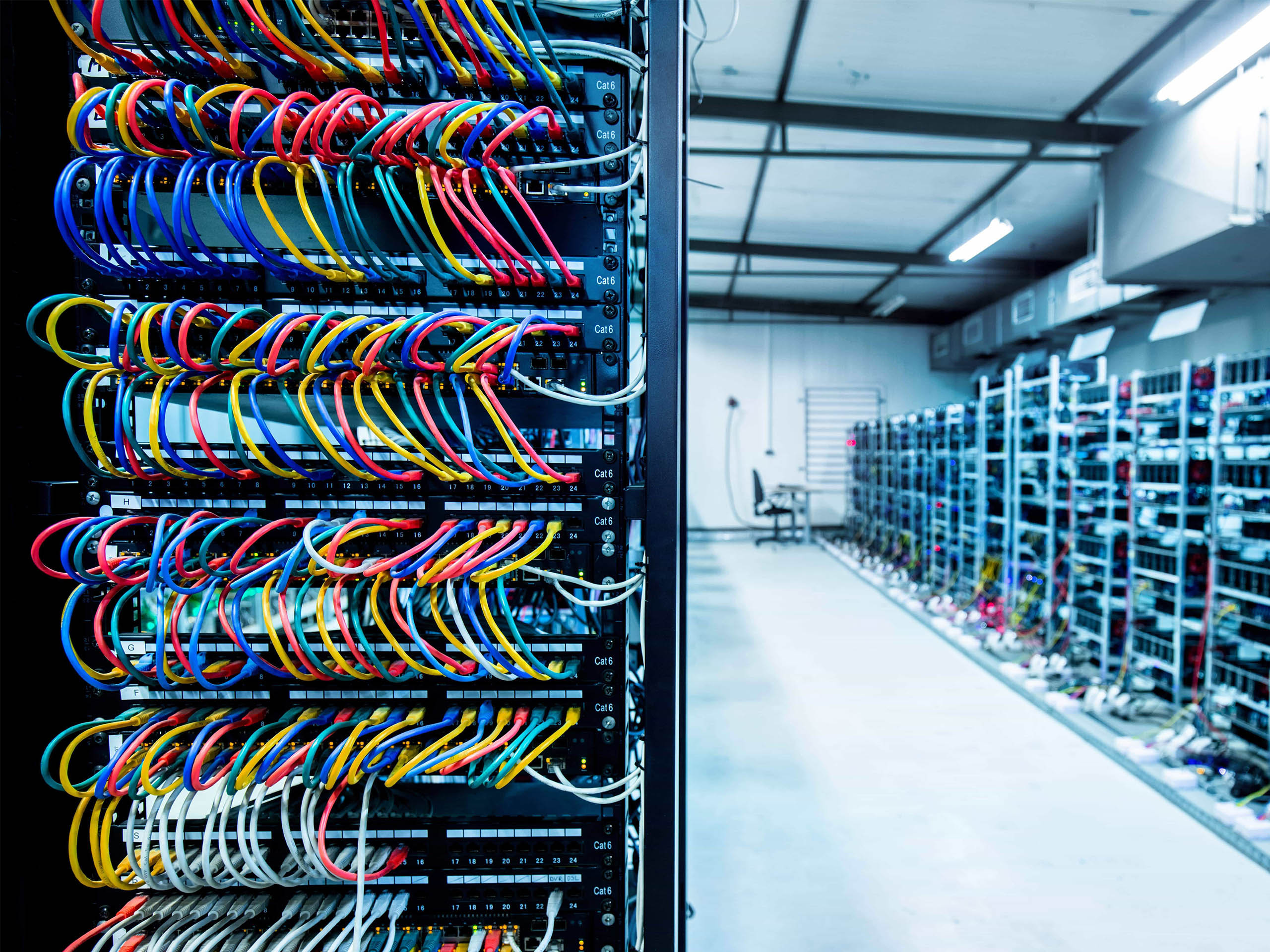
We’re exploring the integral role of plastic extrusions in data centre infrastructure during the meteoric expansion of AI.
A recent report claims data centres consumed an estimated 460 terawatt-hours (TWh) of electricity in 2022. That’s 2% of all electricity use worldwide – and this figure is projected to rise sharply, potentially doubling by 2026 and tripling by 2028, due to the ever-increasing computational power needed for artificial intelligence (AI).
While still in relative infancy, the impending AI boom will skyrocket the global need for processing power. As data centres expand to accommodate this new demand, we’re focusing on an integral infrastructure component: the high temperature-resistant plastic extrusions vital for a data centre’s safety, efficiency, and reliability.
Engineering-Grade performance
The data centre environment is characterised by high heat loads, stringent safety requirements, and the need for robust, durable infrastructure. As mission-critical environments, data centres house intricate webs of high-voltage electrical systems that power complex AI operations. Here, extrusions play a crucial role. Meticulously designed to shield cables, wires, and delicate electronic components, they create barriers that prevent potentially catastrophic short circuits. This equipment protection ensures the seamless flow of data-intensive AI processes, highlighting the vital role of plastic extrusions in data centre safety and reliability.
Although we provide a number of components for data centres, such as cable management and trunking units, we have a unique focus on producing specialised, engineering-grade thermoplastic insulators for busbars within electrical conduits.
Busbars, the copper or aluminium units responsible for carrying the high-energy current required to power servers, must be securely housed in aluminium casings. Our linear extrusions, manufactured from a cutting-edge blend of polymers, insulate these busbars within their housings, preventing the conductor from coming into contact with the aluminium housing, which would otherwise make the entire structure live with electricity.
As insulating high-wattage electricity generates significant amounts of heat, our electrical insulating materials have a high Relative Thermal Index (RTI) value to ensure heat resistance and the integrity of electrical systems, even under extreme conditions.
Cost-Effective Innovation
We can work directly with our partners to pick the most precise material for their needs — whether for an application that requires high-impact or high-temperature resilience or fire retardance — to ensure there is no need to balance performance with financial restraints.
Plastic extrusions offer a compelling solution in comparable electrical safety properties at a fraction of the cost compared to traditional components. This affordability does not compromise on quality; in fact, our advanced plastic polymers are continually being developed to meet the evolving needs of data centres, achieving substantial cost savings without sacrificing safety or performance.
Sustainability in Focus
As the world grapples with the environmental impact of technology, the plastics industry is increasingly prioritising sustainability.
There’s no denying that plastic is an essential part of our daily lives, found all around us. The key is focusing on how we reuse and recycle it responsibly. At Condale Plastics, we are committed to reducing the use of virgin materials in our products, contributing to a circular economy, and minimising waste.
Our unique blend of thermoplastics offers the advantage of being re-processable, as our extrusions can be re-chipped, melted, and reused in-house. Unlike thermosetting plastics, such as tyres, which can’t be reheated. According to legislation, all recycled content must be traceable to ensure quality and adherence. While industry regulations, such as UL certifications, limit the amount of recycled content we can incorporate, we currently reintegrate up to 15% recycled materials, primarily from our own production scrap. This helps prevent waste from going to landfills while maintaining strict compliance with fire-retardant and safety standards.
Our commitment to sustainable design aligns with environmental goals and makes sound economic sense, as it reduces material costs while addressing concerns about the environmental impact of growing energy demands in data centres.
Extrusions in the Evolving AI Landscape
As AI continues to reshape the technological landscape, we’re already actively collaborating with our partners to prepare them for explosive growth.
Our plastic extrusions’ exclusive properties and manufacturing precision are essential for ensuring safe and efficient data centre operation. And we’re not merely keeping pace with data expansion; we’re innovating materials and evolving to stay ahead of the steep curve.
Understanding the value of extrusions can empower informed decisions about data centre design and maintenance, safeguard investments in the AI boom, and provide critical solutions to the challenges ahead.