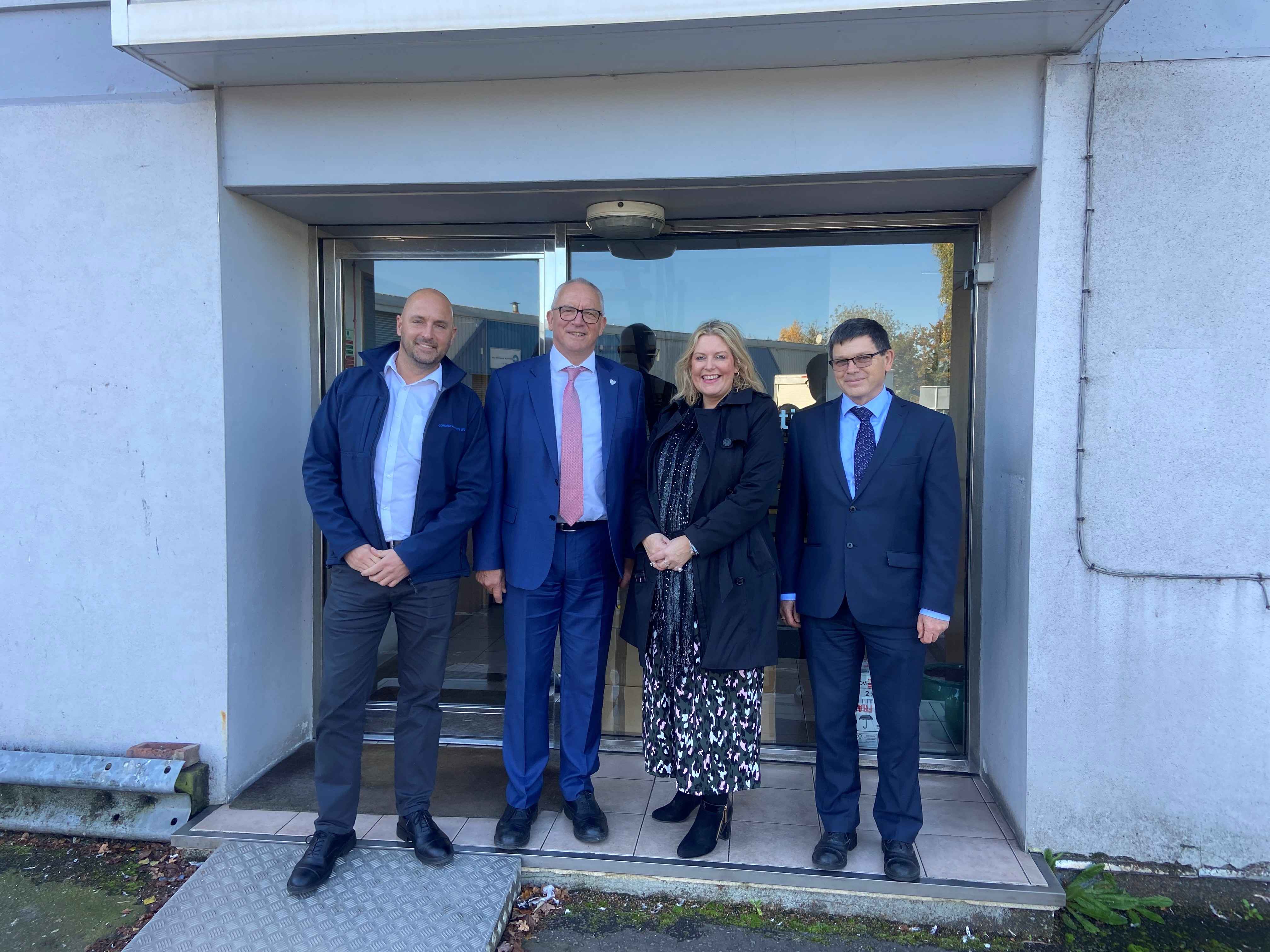
On a recent sunny autumnal Friday, Mims Davies MP, a long-time advocate for education and workforce development, visited our headquarters and factory in East Grinstead. During the tour of our 6,000 square metre manufacturing facility, we showed Mims our state-of-the-art tool room and 33 extrusion lines, as well as a separate clean medical unit for the production of medical grade extrusions.
Mims expressed a keen interest in the multitude of uses for our plastic extrusions and met with some of our longest-serving workers, whose high level of expertise and dedication goes into every aspect of their production. Her visit gave us a platform to discuss one of the most critical challenges facing the manufacturing industry today: the widening skills gap.
The Skills Gap: A Pressing Concern for UK Manufacturing
The UK manufacturing sector has long been an essential contributor to the national economy, accounting for 8.8% of total UK economic output and 7% of all employment between April and June 2024. However, it could face a significant skills shortage in the coming years.
According to Make UK’s (formerly the EEF) reports, in Q1 2024, around 74,000 vacancies remain unfilled in manufacturing, resulting in a £6.5 billion shortfall in economic output.
Despite some regions, like Yorkshire and the South West, seeing a boost in manufacturing employment, the industry still faces labour challenges and is struggling to attract new talent, particularly in highly skilled roles, in the Southeast of England.
As industries continue to grow and innovate with advancements in materials and technology, the demand for skilled workers in fields like toolmaking, plastics extrusion, and engineering has skyrocketed. Filling these roles is crucial for maintaining productivity and innovation; however, educational systems are struggling to keep up with the needs of the industry. As younger generations are drawn to careers in sectors such as finance, media, or IT, they leave a vacuum in hands-on, technical industries.
With an ever-increasing demand for skilled workers, this skills gap is an opportunity for young people to forge exciting careers in specialist roles and for the manufacturing economy to level up, given a supportive governmental policy framework.
We were keen to utilise Mims Davies’ visit to discuss ways to support the local economy and the next generation of technical workers and engineers through training and apprenticeships.
Apprenticeships: A Pathway to Closing the Gap
The disappearance of practical engineering courses that once fed talent into the local workforce leaves manufacturers, such as us, struggling to fill highly skilled positions. Apprenticeships are a key solution for this.
Mims Davies MP has been a strong supporter of apprenticeships, and our discussions reinforced her commitment to this cause. Apprenticeships offer a tangible solution to the skills gap, providing on-the-job training that allows individuals to develop real-world skills while earning a wage. Apprenticeships also offer a viable alternative to traditional university education, particularly for those who may not thrive in an academic environment but have a passion for working with their hands or an interest in technical fields.
Mims shared a personal story during the visit about her own daughter choosing an apprenticeship over university. Despite initial reservations from family members, the apprenticeship allowed her daughter to gain hands-on experience, earn a degree, and make a competitive salary—all without accruing student debt. This story resonated with our team, who see great potential in expanding apprenticeship programmes to attract young people into technical roles that are in high demand.
We believe apprenticeships are a crucial tool in ensuring the future of the manufacturing industry. However, as highlighted during Mims’ tour, we face challenges in formalising apprenticeship programmes. While we’ve hired young workers and provided them with hands-on training, our next critical step is creating a structured, certified apprenticeship programme. This would provide a clearer pathway for young people to enter the industry and ensure that they receive the necessary skills and qualifications to thrive in their roles.
Working Together: Schools, Industry, and Government
One of the key points raised during our discussion was the importance of fostering stronger connections between schools, local businesses, and government agencies like the Department for Work and Pensions (DWP). Mims shared examples of successful initiatives from other parts of the country, such as Scunthorpe, where business leaders worked directly with local schools to create business ambassador programmes. These programmes introduced students to the career opportunities available in their own communities, helping to break the misconception that they need to move to larger cities like London to find a fulfilling career.
Mims said, “You don’t need to move to the big cities to have a great career. We need to open up the mindset about what local careers can really look like, especially for young people who aren’t on a traditional academic path. Intervention at the right time can make all the difference.”
The concept of business ambassadors resonated with us, as we’re already active in our local community, hosting work experience opportunities and school visits. However, more can be done to create long-term partnerships with schools, ensuring that students are aware of the career paths available in manufacturing from an early age. Bringing young people into the factory for tours or work placements can be eye-opening, particularly when they see the complex machinery, learn about the science of materials, and meet the experienced workers who keep everything running smoothly.
During the visit, Mims also highlighted the role of the DWP in supporting businesses like ours through initiatives such as Sector-Based Work Academies. These academies provide six weeks of training and learning with an employer, giving individuals a taste of what a career in manufacturing might be like. Through Mims, we’re looking forward to connecting to our local DWP team to help bring in new candidates, particularly those who may not have considered manufacturing as a career but are eager to learn and grow in a practical environment.
A Bright Future: Expanding Opportunities for All
As the visit came to a close, Mims and our team discussed the broader implications of expanding apprenticeships and addressing the skills gap. In addition to bringing young people into the industry, there is also a need to diversify the workforce. Manufacturing, traditionally male-dominated, has made strides in recent years in attracting women to the sector, but more can be done. At Condale Plastics, we’re keen to continue this progress, having recently hired our first female workers in setting roles on the shop floor.
Mims was particularly interested in how apprenticeships could be tailored to attract a more diverse workforce, ensuring that manufacturing is seen as an inclusive, rewarding career path for everyone. By creating apprenticeship opportunities that appeal to a wide range of candidates—whether they are young people starting their careers or career changers looking for a fresh start—we can help ensure that the manufacturing industry remains strong, resilient, and innovative for years to come.
Our Managing Director, Michael Stewart, said: “Building and sustaining a skilled workforce is essential to our business’s long-term success. Mims highlighted initiatives which can help attract new local talent to the industry. Collaboration among local businesses, schools, and government agencies will be key to securing a strong future for UK manufacturing.”
Mims Davies MP’s visit was a testament to Condale Plastic’s commitment to bridging the skills gap and expanding opportunities through apprenticeships. With the support of government initiatives, local schools, and forward-thinking businesses like ours, the future of manufacturing in the UK looks bright. By working together to promote apprenticeships, provide training, and encourage a diverse range of individuals to enter the industry, we can build a skilled workforce that is ready to meet the challenges of tomorrow.
Find out more about how we craft bespoke extrusions by downloading our brochure: Brochure Download – Condale Plastics